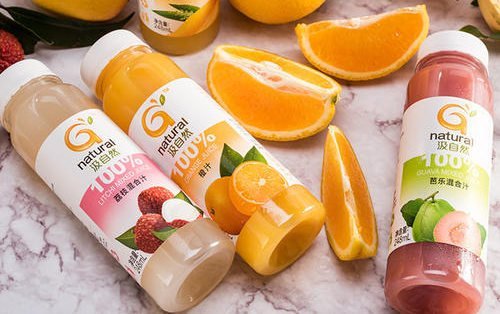
[lwptoc min=”2″]
Table of Contents
Toggle- Hot Filling Definition
- Products Suitable For Hot Filling
- Juice&Energy Drink Hot Filling Line Process
- Problems To Be Considered In Hot Filling ‘Bottle’
- Empty Bottle Treatment.
- Empty Bottle Rinsing
- Empty Cap Treatment.
- Empty cap treatment.
- Filling Method
- Material Treatment
- Bottle Tilting Sterilization System
- Sterilization&Colling Tunnel
- Filling Machine CIP
- Filling Machine SIP
- Filling Machine COP
Hot Filling Definition
- Cool the pasteurized beverage to 83-95 ℃, then fill and seal it into a container. After a certain period of time, kill the microorganisms in the container and on the cap, so that the beverage can be transported and stored at room temperature during the shelf life.
- The beverage with pH value ≤ 4.6 after sterilization is suitable for hot filling process.
Products Suitable For Hot Filling
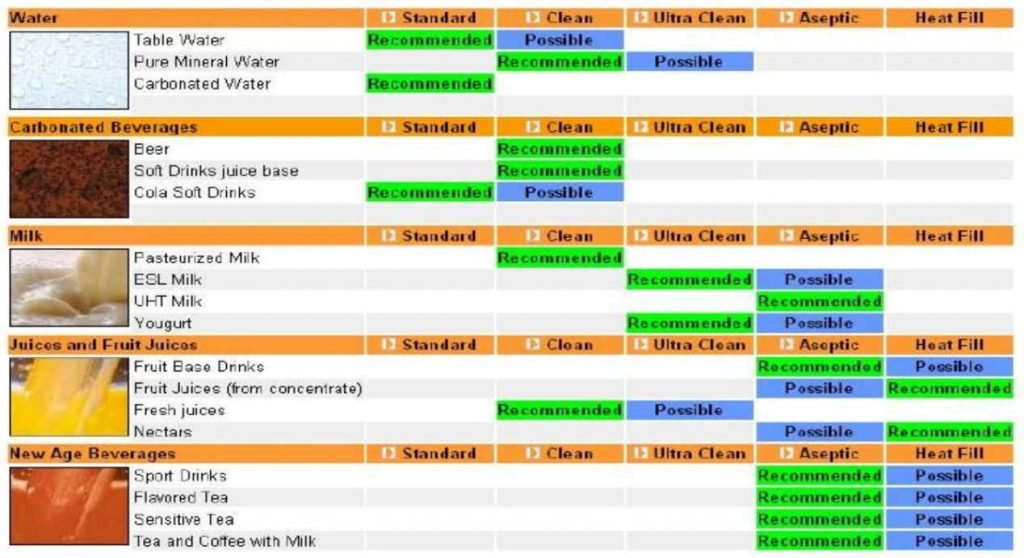
Juice&Energy Drink Hot Filling Line Process
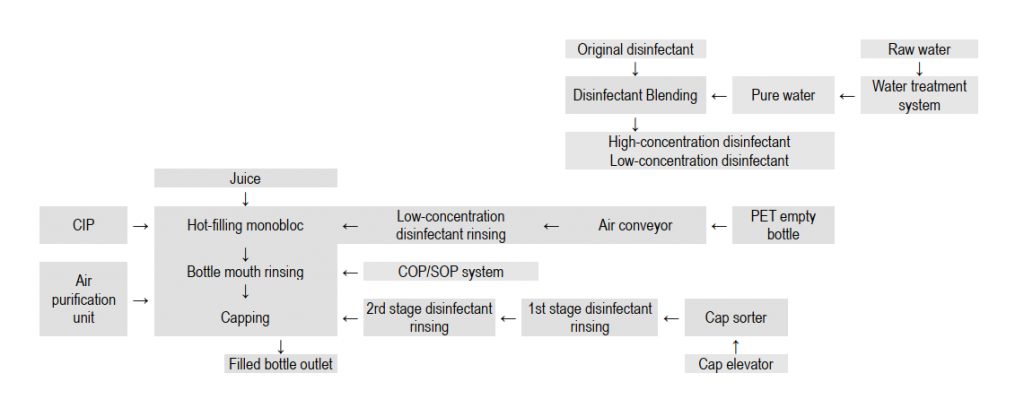
Problems To Be Considered In Hot Filling ‘Bottle’
Glass Bottle Hot Filling
If use glass bottle, the glass bottle should generally be warmed before entering the hot filling machine, so that the difference between the temperature of the glass bottle and the hot filling temperature is less than 40 ℃, so as to ensure that the bottle will not burst due to the excessive temperature difference.
PET Bottle Hot Filling
The basic technological requirements of hot filling (85℃-95℃) for plastic (PET, BOPP) bottles are as follows:
- The internal pressure of the bottle will increase within 30 seconds after sealing.
- The bottle shrinks at high temperature.
- When the temperature of the product falls back to room temperature, the volume of the liquid will be reduced by 2% to 3.5%. The drop in temperature will also increase the solubility of the air, so that the steam will be condensed, and the air pressure in the bottle will drop slightly (20~30Pa).
Hot Filling Bottles Should Have The Following Characteristics:
- The bottle must be heat-resistant (preferably above 90 ℃), and the volume reduction of the bottle must be less than 3% under high temperature filling.
- Strong barrier, low water absorption, maintain product quality.
- The thickness distribution of bottle wall should be appropriate to avoid nonlinear shrinkage after filling.
- The bottle body and bottom are specially designed (reinforcement) to reduce the decompression caused by the decrease of liquid volume during cooling.
Empty Bottle Treatment.
Empty bottle requirements before disposal.
Project | Index |
Total bacterial count | ≤ 50 CFU/ bottle |
Mold and yeast | ≤ 20 CFU/ bottle |
Pathogenic bacteria shall not be detected. | |
There shall be no oil, impurities, dust, insects and other foreign bodies on the internal and external surfaces of foreign bodies. |
Empty Bottle Rinsing
- Removal of foreign bodies inside empty bottles.
- Reduce the number of microbes in empty bottles
Empty Bottle Treatment.
Rinsing requirements for empty bottles.
- Rinsing pressure > 2bar.
- Rinse water covers the inner wall of the bottle.
- Intermittent spray flushing.
Empty bottle microbial sterilization.
- Material waste heat.
- 82 ±1 ℃
Empty Cap Treatment.
Pre-processing empty cover requirements.
Project | Index |
Total bacterial count | ≤ 50 CFU/ cap |
Mold and yeast | ≤ 20 CFU/ cap |
Pathogenic bacteria shall not be detected | |
Foreign body clean and hygienic, no dust, oil stains and other foreign bodies, no irritating odor |
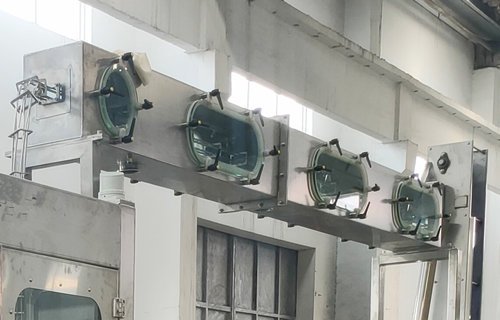
Empty cap treatment.
- Rinse the bottle cap with disinfectant.
- Concentration: for example, [Cl-] = 200 ±20ppm.
- Rinsing pressure ≥ 2bar.
- Spray pressure ≥ 2 bar- Clean compressed air blow-dry bottle cap
Filling Method
Through the filling mode of gravity filling and negative pressure reflux, the filling capacity of the filling machine can be increased in the case of the same number of filling valves.
Liquid level control
Hot filling requires PET bottles to have a higher liquid level or full bottle after filling, in order to reduce the impact of oxygen in the residual air in the gap at the mouth of the bottle on the quality of the beverage. The hot air of the bottle mouth material can also replace some of the air, which is beneficial to the bottle tilting system in the later process to sterilize the bottle mouth and the inside top of the bottle cap, so as to further ensure the quality of the beverage.
Bottle Mouth Rinsing Process.
- Bottle mouth flushing devices are respectively installed on the star wheel of the bottle rinsing machine and the star wheel of the capping machine.
- Disinfect the thread part of the bottle mouth.
- Rinse the threaded part of the bottle mouth. Avoid mildew spots on the screw thread of the bottle mouth for a period of time after capping, which will affect the quality of the drink.
Backflow Process
External reflux of the machine.
When the material is sterilized by UHT and sent to the filling machine, if the temperature of the material is lower than the set value, the material is returned from the pipe outside the valve to UHT for reheating and sterilization, which effectively controls the filling temperature.
Backflow in filling process.
In the process of hot filling, a certain negative pressure is produced by the exhaust fan, and the air and foam in the bottle are quickly sucked away in the filling process, which not only improves the filling speed, but also solves the half-bottle phenomenon. At the same time, it also effectively avoids the bottle body bulging and material overflow caused by other filling methods.
Backflow in filling valve without bottle. The shutdown of the machine for various reasons in the filling process may lead to the decrease of the material temperature in the feeding cylinder and valve. At this time, through the reflux path inside the filling valve, the material can still flow according to the filling process with a certain flow rate, so that there are new materials in the feeding cylinder and filling valve, and the temperature of the material is kept within the required range to meet the requirements of real hot filling.
Material Treatment
- UHT processing.
- Set sterilization parameters according to the characteristics of microorganisms in the product.
- For example, 95 ℃, 130 ℃, 5~30sec
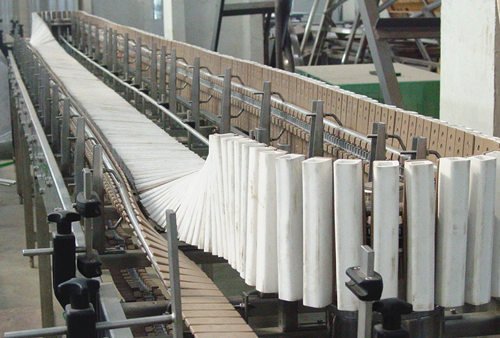
Bottle Tilting Sterilization System
- The main purpose of the bottle tilting sterilization chain is to tilt the product after filling and sealing, and make use of the temperature of the product itself to sterile the bottle cap.
- The second sterilization is carried out to soften the sealing gasket of the bottle cap and improve the sealing degree between the bottle cap and the bottle body.
- Bottle filling time is usually more than 30s, after sterilization, the conveyor chain is automatically righted, and the product enters the next process.
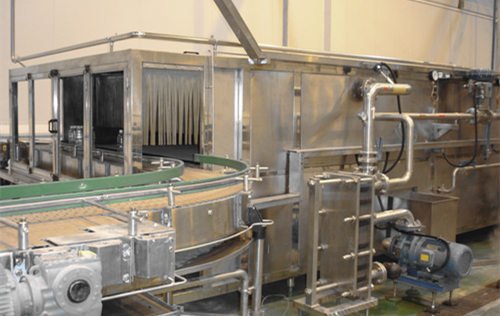
Sterilization&Colling Tunnel
- Step cooling.
- To prevent excessive deformation of the bottle.
- Outlet temperature 40 ℃.
- Water evaporation on the outer wall of the bottle.
- It will not damage the quality of the product.
- Last rinse with soft water.
- Reduce the water marks on the outer wall of the bottle.
- The spray water is all RO water, and the external refrigerant is changed for heat treatment.
- Some products also need to add a period of heat preservation and sterilization.
Filling Machine CIP
- Fake cup cleaning
- Automatic installation or manual installation.
- Remove the organic and inorganic matter inside the equipment; improve the germicidal efficacy of the equipment.
- Mechanical principles or chemical principles.
- At the end of production during the operating period or before the start of production
Filling Machine SIP
- Sterilization Point.
- Line from UHT, filling machine, UHT to filling machine.
- Sterilization method.
- Hot water sterilization.
- 85 ℃ 130 ℃. 30min
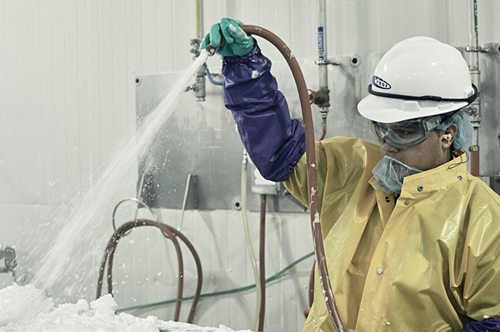
Filling Machine COP
- Maintain a good production environment.
- Cleaning with foam cleaner.
- Chemical action.
- The bursting power of bubbles.
- Operation period: after the end of production
Now if you want to produce your own hot filling beverage (juice, energy drink, water, etc), and want to import hot filling machine from Chinese manufacturer, Festa will be your best choice. Our professional engineer team has more full experience to deal with this hot filling project and will help you design the complete hot filling line according to your budget and requirement.
Just fill out blew form and let us know your idea, we will reply to you within 11 hrs.