Advanced Aseptic Filling Machine Manufacturer
- Compatible with different liquids, fruit juices, liquid milk, beverages, etc, on the same machine.
- Extend the shelf life of the product without adding preservatives
- Provide separate aseptic bottle filler, can also manufacture aseptic blowing filling capping combiblock.

FESTA Aseptic Filling Technology Rocket Your Business
Aseptic filling: it is the most advanced technology for the filling of PET bottles with sensitive beverages, 25-30 ℃ filling temperature, which can keep the product nutrition, color, taste etc. as much as possible and can help customer to save a lot of raw material and energy cost, suitable for both high and low acid products.

WJG18-18-18-18-6 Aseptic Bottle Filler
This is the small scale aseptic filling machine that we specially developed for the market. It is a standard aseptic filling system, but the production capacity is very suitable to meet the urgent needs of enterprises for aseptic filling line miniaturization.
- Production Capacity: 6000BPH(500ml), 4000BPH(1L)
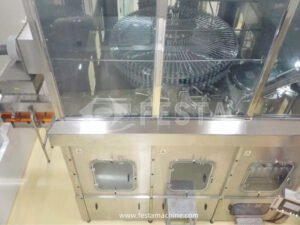
WJG40-40-40-24-8 Aseptic Filling Machine
FESTA WJG40-40-40-24-8 adopts 5-in-1 aseptic filling technology. Include two disinfectant rinsing process, one aseptic water rinsing process, one aseptic filling and aseptic capping system. This is the best choice for many enterprises to enter the field of aseptic filling.
- Production Capacity: 12000BPH(500ml), 6000BPH(1L)
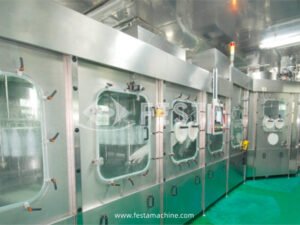
WJG72-72-60-50-10 Aseptic Bottle Filling Equipment
The use of wet aseptic filling technology, for all packaging materials (empty bottles, lids) more thorough sterilization, higher safety. Production capacity is also the current mainstream 333BPM, suitable for most high-end beverage filling factories.
- Production Capacity: 20000BPH(500ml), 13000BPH(1L)
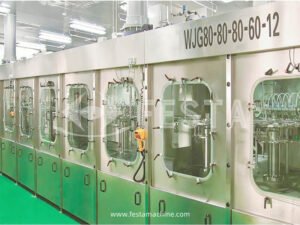
WJG80-80-80-60-12 Aseptic Liquid Filling Machine
At present, this model is the preferred production capacity of many international famous beverage companies, which can fill 400 bottles per minute. A mature five-in-one aseptic filling system is adopted. Aseptic capping machine adopts the mainstream products of AROL company, which is stable and reliable.
- Production Capacity: 24000BPH(500ml), 16000BPH(1L)
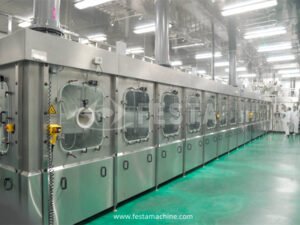
WJG90-90-90-80-18 Aseptic Filling System
FESTA WJG90-90-90-80-18 is an epoch-making aseptic bottle filling machine developed for famous beverage companies in the industry.
- Production Capacity: 30000BPH(500ml), 20000BPH(1L)
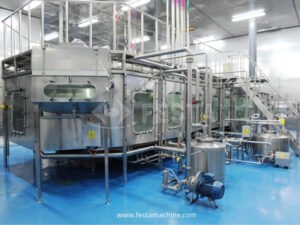
WJG100-100-90-90-25 Aseptic Bottling Machine
WJG100-100-90-90-25 is a FESTA high-speed aseptic filling system, which adopts the most mature wet aseptic filling technology, and the beverage produced has no loss of nutrition and good taste.
- Production Capacity: 36000BPH(500ml), 24000BPH(1L)
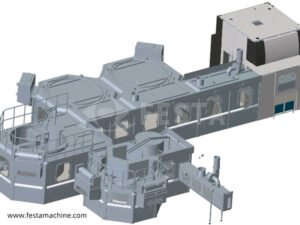
WJBFC12-80-80-80-60-15 Aseptic Blower Filler Capper Combiblock
With the development trend of intelligent and high-speed aseptic filling line, we combined our own advantages and launched the aseptic combi system. Cancel the traditional aseptic air conveyor link bottle blowing machine and aseptic filling machine. Greatly reduce the occupied area and investment cost.
- Production Capacity: 24,000 bottles per hour based on 500ml bottle
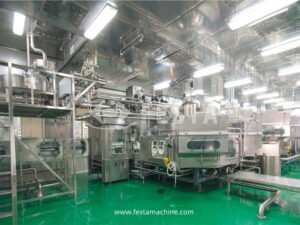
WJBFC18-90-90-90-80-20 Aseptic Combi(Blowing Filling Capping)
600BPM aseptic combi is the highest speed and most advanced aseptic solution in our company. It can be used for filling almost all liquids without adding any preservatives. If you are interested, make an inquiry with us now.
- Production Capacity: 36000 bottles per hour based on 0.5litre bottle
Related Equipment of Aseptic Filling Line
FESTA Aseptic Filling Machine Boost Your Beverage Brand Value
Filling at room temperature can minimize the heating time of the beverage, reduce the loss of vitamins and enrich the nutrition, and keep the original taste of the beverage product. Because of the normal temperature filling, the aseptic bottle type does not have to design reinforcement to prevent the bottle from being deformed by hot liquid like hot filling bottle, so the enterprise is free to design the bottle type and enhance the brand image of the enterprise. Enhance market competitiveness.
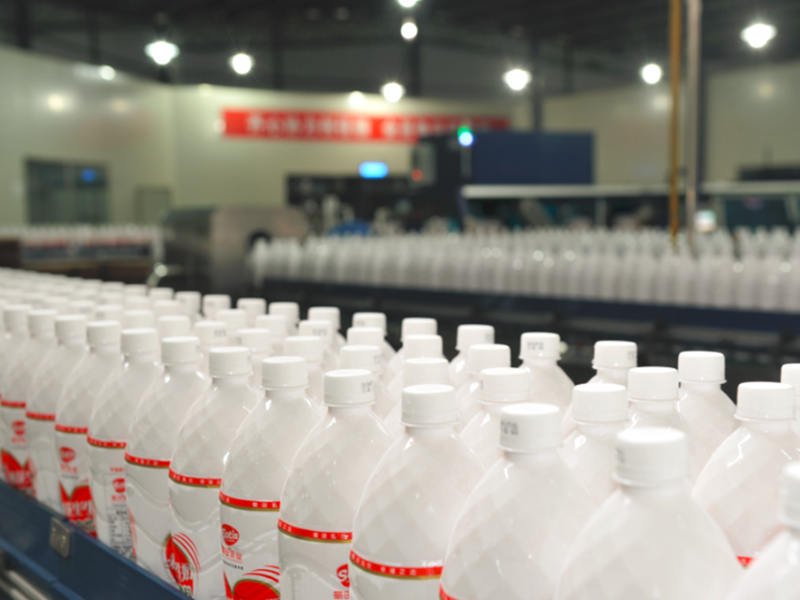
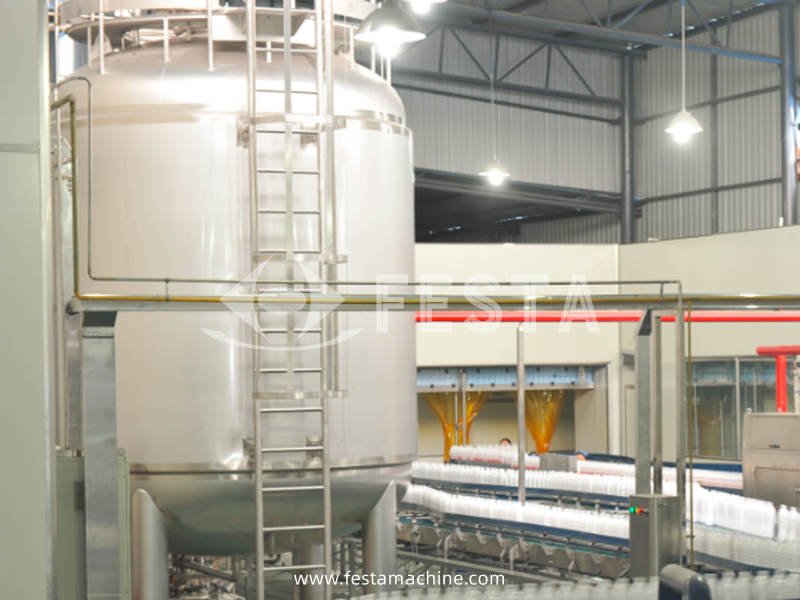
Use FESTA Aseptic Filler to Reduce Your Production Costs
Compared with hot filling, the packing material cost of bottles and caps can be reduced by 1/2 to 1/3. Due to the cancellation of the cooling and showering tunnel, there is no need for long full bottle conveyors, and the energy consumption can be reduced by 1/3. The comprehensive cost is reduced a lot, which is beneficial to improve the competitiveness of your products in the market.
Flexible Aseptic Bottle Filling System for All Liquid
Aseptic cold filling can adapt to a wider range of products, such as mixed tea, milk tea, pure milk and protein drinks, wine, mineral water, carbonated drinks and so on. Aseptic filling system can also add particle filling system, almost all drinkable liquids can be aseptic filling.
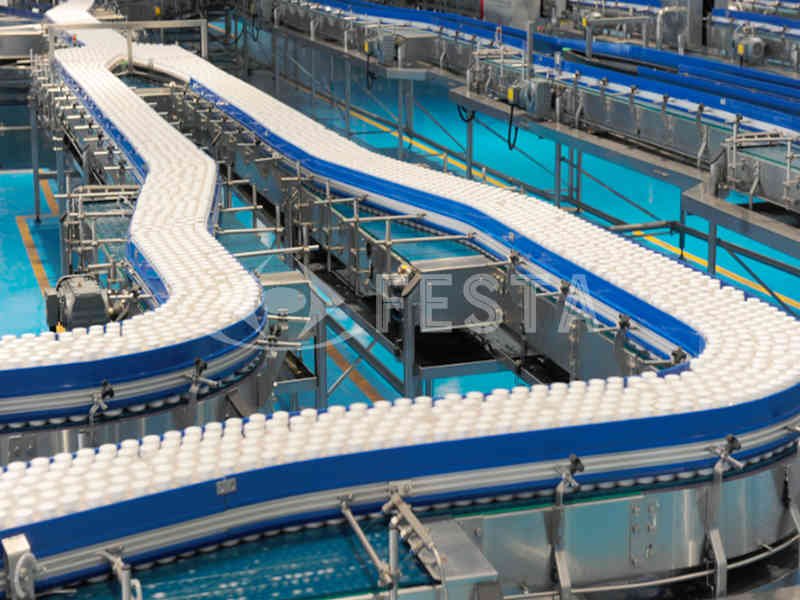
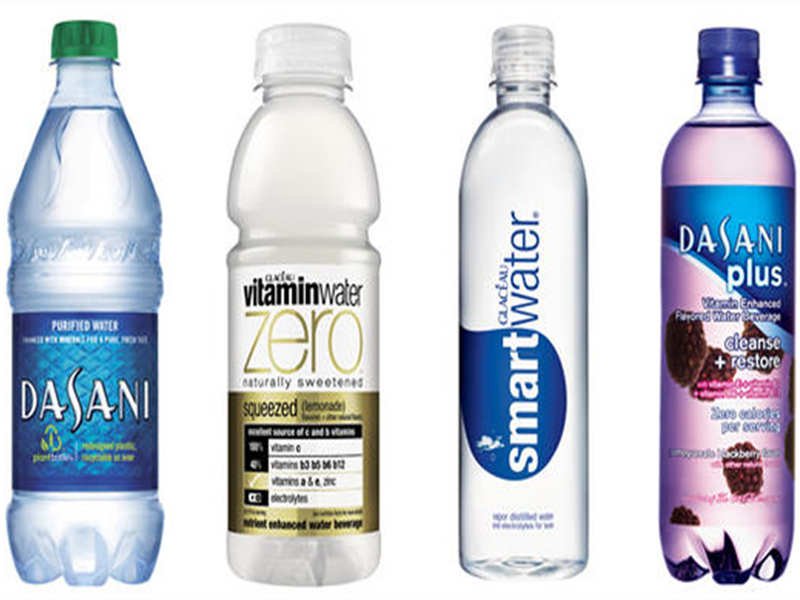
FESTA Automatic Aseptic Liquid Filling Machine Video
If you want to know more about our aseptic filling system solution, contact our team now!
Visit Our Aseptic Filler Factory in China
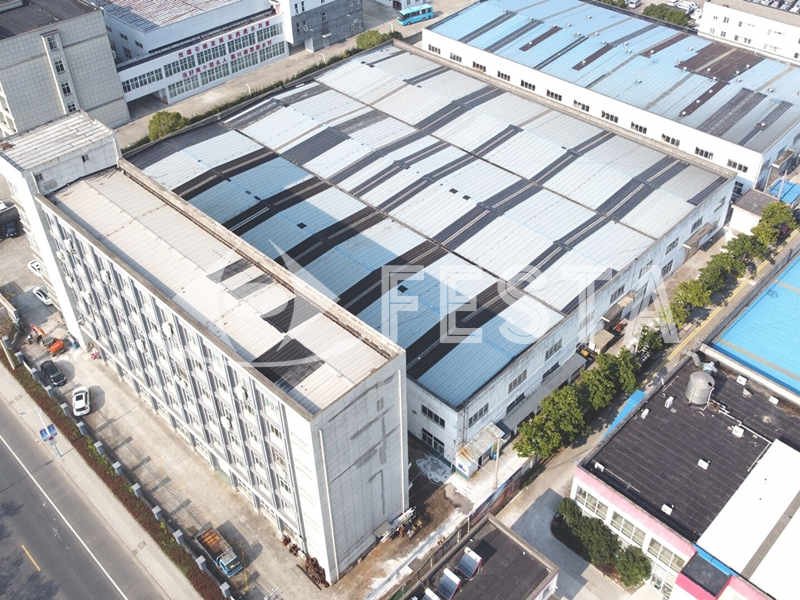
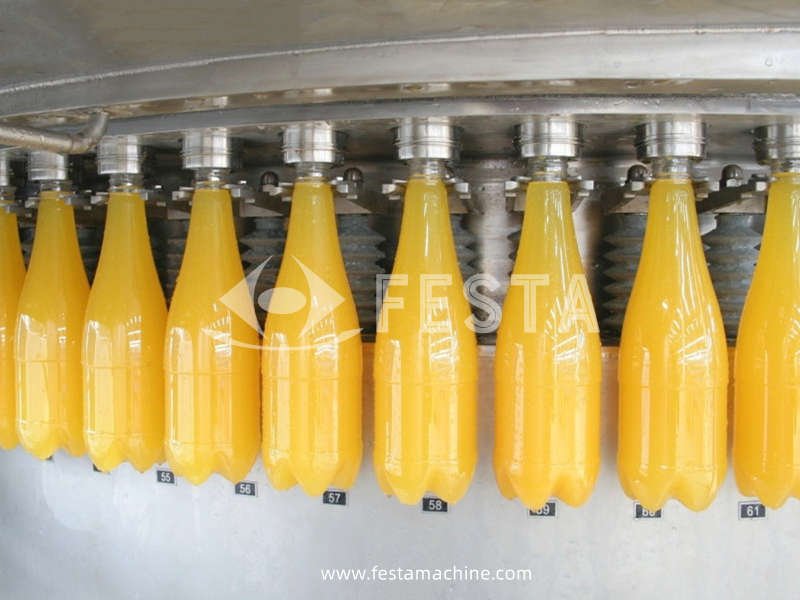
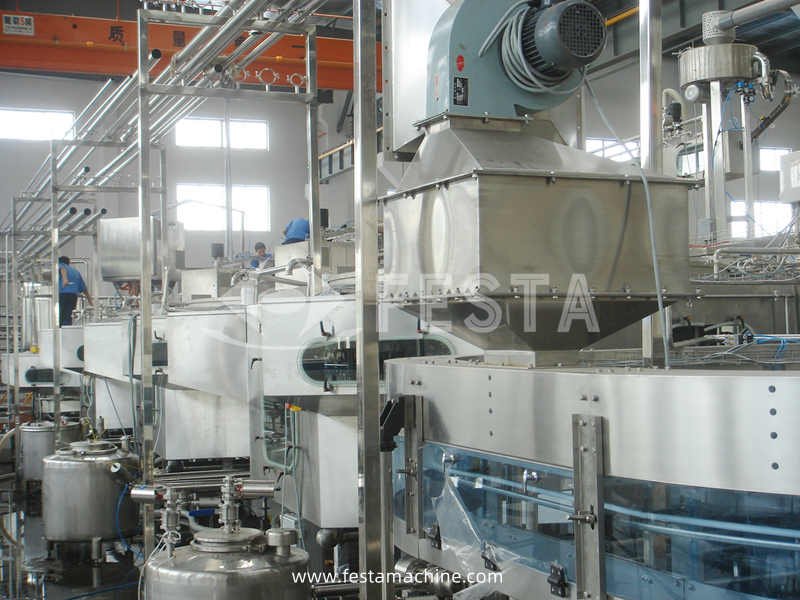
The Definite Guide of Aseptic Filling Machine
Definition: No any microorganism surviving.
But current technology can’t meet the above requirement completely.
What aseptic filling can do: Commercial sterility (Customer can accept that there is only one bottle defect product per 10,000 bottles.)
That is, control the microorganism under the expected range, which won’t harm to our body and affect product quality. In terms of the soft drinks, it is almost reaching absolute sterility standard.
Sterilizing Efficiency
LCR can be taken as Sterilization Efficiency (SE)【also called “Killing Power”】
Product
- Natural product
- Low thermal impact
- Little change in color
- Little change in flavor
- Better protection for the valuable ingredients (vitamin etc.)
Bottle
- Light-weight, unbreakable and transparent PET bottles
- Flexible bottle design
- Low bottle / preform price
From the comparison table below, you can see that the advantage of aseptic filling machine is that it can save production costs from all aspects.
Item | Hot filling | Aseptic filling |
Initial cost | Minor initial investment | Significant initial investment |
Container costs | Heavy bottles (28-32g/0.5l) and caps: higher costs (crystallized neck requested in case of filling temperature higher than 85 ℃) | Lightweight bottles(18-23g/0.5l) and caps: lower costs |
Running costs | Hot-fill blower (high compressed air consumption), tilter and cooling tunnel are requested: higher energy consumption | Normal blower (less compressed air consumption), no need tilter and cooling tunnel: lower energy consumption |
Personalized containers | Scare possibility of personalized bottles | Personalized bottles without any limitations |
Product treatment | More invasive and longer time thermal treatment on the product (especially in the event of an increase in the rate of product recirculation) | Minor thermal treatment on the product, keep flavor, color, nutrition of production as much as possible |
Filling temperature | 85-95℃ | 25-30℃ |
Critical point | Filling temperature and filling environment | Sterilization of beverages and packages, sterilization and maintenance of machines and environment |
Operator requirement | The line can be run by operators with basic line experience | The line must be run by highly skilled line operators |
Shelf life | Long shelf of the product (up to 1 year) | Long shelf of the product (up to 1 year) |
Applicable range | Limited range: high acid product (Juice, gree/black/Olong tea, black coffee, sports drinks) | Big range: high acid to low acid product (Juice, green/black/olong tea, barley tea, black coffee, sports drinks, milk tea, coffee milk, flavor/white milk.) |
(1)Disinfection of bottles, caps and equipment.
(2)Eliminate processes that may cause microbial or chemical contamination of the product.
Commonly used methods of bottle disinfection
- Wet PAA, rinse the bottle inside and outside with disinfectant and rinse with sterile water.
- Vaporize PAA, activate PAA with steam, fully cover the inner wall of the bottle, rinse with water.
- Vaporized hydrogen peroxide, steam vaporized hydrogen peroxide, flushed with sterile water.
Commonly used methods of bottle cap disinfection:
- PAA immersion.
- Atomized hydrogen peroxide disinfection.
- Empty bottle PAA sterilization and rinsing system, aseptic system capable of aseptic filling and capping.
- Bottle cap sterilization system.
- Environmental pollution control system.
- A series of process systems that can provide qualified necessary fluids (water, gas, materials)
In the aseptic filling system of FESTA, in order to achieve the aseptic goal, the following functions are mainly applied:
- Create and maintain a sterile environment for aseptic filled products.
- All pipelines related to product contact or filling go through CIP and SIP.
- Sterilize the surfaces of all containers and lids that come into contact with the product.
- Fill aseptic products.
- Seal the container well.
Bottle: the empty bottle is transported to the filling area through the aseptic air conveyor, and then fed into the bottle by a two-wheels sterilizer. Sterilize and disinfect the bottle, then wash the bottle by the aseptic water flushing machine, and finally enter the filling and capping machine.
The filling machine will be fed through a balancing tank, and the following measures will be adopted to prevent secondary pollution of the product:
- The whole filling pipeline is cleaned and sterilized regularly by CIP/SIP.
- Fill the balance tank of the filling machine with sterile air to maintain the positive pressure in the tank.
- The filling head of the filling machine does not touch the bottle.
Aseptic environment: the sterilization areas of bottles and lids are under the monitoring of the automatic control system.
The role of FFU is to maintain a static pressure higher than atmospheric pressure in the sterile environment so as to prevent external microbial particles from infiltrating into the interior. The inlet air to maintain this static pressure must be filtered by a high efficiency filter before it can enter.
Aseptic products: products will be sterilized by UHT before being sent to the filling area.
Disinfectant: obtained by diluting and concentrating PAA solution and diluting the solution according to volume or weight according to predetermined process parameters.
Aseptic water: made by heating RO water with UHT.
CIP: internal cleaning of the system
Fluid treatment.
Compressed air: it is filtered by a sterile filter. In order to ensure the safety of use, the equipment is equipped with two-stage ultra-fine filter.
Nitrogen: also filtered by a sterile filter.
Steam: steam is also filtered by a sterile filter, but it only ensures that there are no impurities.
Water: mainly rely on sterile water UHT high temperature sterilization.
Supply the corresponding sterile water flushing during production or start-up.
Before starting the filling, the filling area must be commercially aseptic. Therefore, the cycle of disinfection and cleaning must be done before starting up, so as to ensure the asepsis in the production process.
- The aseptic window sealing is adopted and the whole welding method is adopted to minimize the sanitary dead corner.
- Equipped with COP/SOP system, the whole equipment can be cleaned and sterilized.
- The application of water ring liquid seal makes the interior of the filling machine well isolated from the clean room.
- Sanitary work table.
- Aseptic air conveyor bottle inlet or aseptic combiblock
- The power supply adopts multi-gearbox separate transmission or servo transmission.
- Empty bottle transmission adopts bottle clip transmission pulley.
- The bottle is flushed three times, that is, twice disinfectant and once aseptic water, and the flushing is controlled by diaphragm valve.
- The quantitative filling method is adopted by the combination of flow meter, diaphragm valve or Flowmeter with mechanical valve.
- Sanitary capping machine, can clean and sterilize the surface of capping machine.
- The pressure control of each pressure zone is realized by FFU control.
- The waste gas recovery system ensures that the internal smell of the filling machine will not enter the clean room.
Aseptic window sealing.
The microbial isolation bin ensures the aseptic state of the filling area, and aseptic gloves are arranged in some important positions around the machine, which can operate the equipment without destroying the aseptic environment.
COP and SOP
Water ring liquid sealing system
Isolate the clean area and operating area of the filling machine.
The sealed water circulates itself, and fungicides are added to keep it sterile.
- Electric slip ring: provide power for PLC, as well as external signal input and output.
- Gas distributor: provides air source for diaphragm valve.
- Control cabinet: install PLC and other electrical equipment.
- Bottle dispenser: provide disinfectant, sterile water, COP channel.
- Bottle clamp: bottle retention and transfer
The empty bottle is transferred to the bottle washing machine via aseptic air conveyor and then separated by a steel wheel.
The steel clip is then passed to the empty bottle sterilizer, the steel clip is flipped along the guide rail to make the bottle mouth down, and the disinfectant is sprayed on the bottle.
- Main distributor: provide material, aseptic gas, CIP, COP and other channels.
- Electric slip ring: same bottle punching machine.
- Gas distributor: same flushing machine.
- Control cabinet: install PLC.
- Flowmeter: measure the filling volume.
- Fake cup: CIP reflux during cleaning.
Using Flowmeter constant volume filling, there is only one valve in the whole pipeline, and non-contact filling can be used to avoid the spread of pollutants through the valve head.
- Capping head: used for capping.
- Lifting assembly: provides power for the capping head, and rises and falls along the cam surface.
- Cam: provides the motion track corresponding to the bottle cap.
- Basic parts: provide power for the operation of the capping machine.
Design of aseptic capping machine for FESTA at present.
- In the way of thermal barrier, each capping head has a thermal barrier to rise and fall.
- The moving part and the capping head are isolated by diaphragm protection.
- The whole capping machine is in the isolation area of the filling machine, which has requirements for the materials of many parts.
- In the servo-controlled capping machine, the capping machine is realized by the rotation of the servo motor, the torque of each capping head can be monitored in real time, and the torque parameters can be modified online on the touch screen.
Capping machine lifting assembly.
Sanitary structure, surface washable.
Constant torque aseptic capping head.
- Sanitary structure, hollowed-out way of drainage, no fluid accumulation.
- The operation of the capping head is stable, which weakens the factors causing the vibration of the machine.
Capping machine cam.
- Special materials, corrosion resistance, wear resistance.
- Optimize the cam curve and make the exclusive design for the corresponding bottle cap.
Basic parts of capping machine.
- As a support for capping parts (cam, capping head, lifting assembly).
- Provide power for the capping machine.
- Adjust the transfer position of the bottle.
The environment controlled by aseptic filling machine is composed of the following parts: bottle entry transition zone, two-wheel disinfectant flushing machine, aseptic water flushing machine, filling machine, capping machine, bottle outlet area, cap disinfector.
The automatic control system can control the pressure difference of each region in a relatively stable state. SOP is carried out regularly to thoroughly sterilize the inner space of the filling machine.
The pressure difference in each area is controlled by the air supply of FFU, and the relevant parameters can be adjusted and set by touch screen or governor.
Waste gas treatment unit.
- Conducive to environmental protection.
- Adjust the pressure of each zone.
Adjust the pressure of each zone by adjusting the opening of the corresponding butterfly valve.
The exhaust gas treatment function can be turned on on the touch screen to neutralize the PAA in the exhaust gas.
Figure 1: before the production of the equipment, the reflux diaphragm valve is opened and is in a state of self-circulation, heating up the valve and pipeline.
Figure 2: when a bottle is detected to start filling, the reflux diaphragm valve is closed, the filling valve is fully open, and it is in a state of rapid filling.
Figure 3: when the Flowmeter detects the set filling volume, the filling valve is switched to small flow filling, which is in a slow filling state to ensure the filling accuracy.
Figure 4: at the end of filling, the filling valve is closed and the reflux diaphragm valve is opened to ensure that the pipeline does not lose temperature; in the state of continuous filling, you can also choose not to return and no bottle to return to reduce the reflux.
Figure 5: automatically rotate the false cup to thoroughly clean the valve as well as the feed pipe and low temperature reflux pipe.
Validation in Lab
- Disinfectant stability test
- Disinfectant sterilizing intensity test
Inspection before validation
- Process temperature inspection system test
- Compressed air anti-bacteria filter integration test
- UHT sterilization holding time test
- ULPA filter and installation test
Process condition validation
SIP process condition and effect validation
- Steam SIP
- Superheated water SIP
- Disinfectant SIP
UHT sterilizing condition and sterilizing effect test
CIP process condition and cleaning effect test
COP process condition and cleaning effect test
- Lyeing experiment
SOP process condition and sterilizing effect test
- Coupons (Microbiological challenge) experiment
Single machine validation
- Sterile water-microorganism test
- Sterile material/product-microorganism test
- Sterile compressed air-microorganism test
- Isolated area-microorganism test
- Bottle/cap sterilizing effect test
Online validation
- Product water test (instead of product)
- LG (Linden Grain) culture media fill test
- Trial production test
If you have a sufficient budget, we highly recommend you to buy some of the best aseptic filling machines in the world.
Krones Aseptic Filling Systems.
If you consider cost-effective, you might as well talk to FESTA. As an aseptic filling machine manufacturer, we always deal with your needs carefully and provide you with one-stop filling line solutions.