12000BPH Blowing Filling Capping Combi BFC6-24-8
Production Capacity: 12000BPH
Control mode: Fully-auto PLC control
Number of mold cavity: 6
Suitable: Bottle water combi, CSD combi, Juice Combi
Benefit of FESTA BFC6-24-8 Blowing Filling Capping Combi
The BFC Series Blowing Filling Capping Combiblock developed by Festa, on the base of “Blowing unit”, “”Filling unit” and “Capping unit”, mixing all kinds fields like optics, mechanics, electrical etc., adopts servo system to realize synchronous control and removes the empty bottle conveying and rinsing part of traditional line, saving production line covering area, energy (water, electricity, air etc.) consumption, operating staff, running and maintenance cost, and meanwhile, improves the hygiene working condition and the whole line efficiency, more eco-friendly. It can be applied in still water, CSD and other soft drinks.
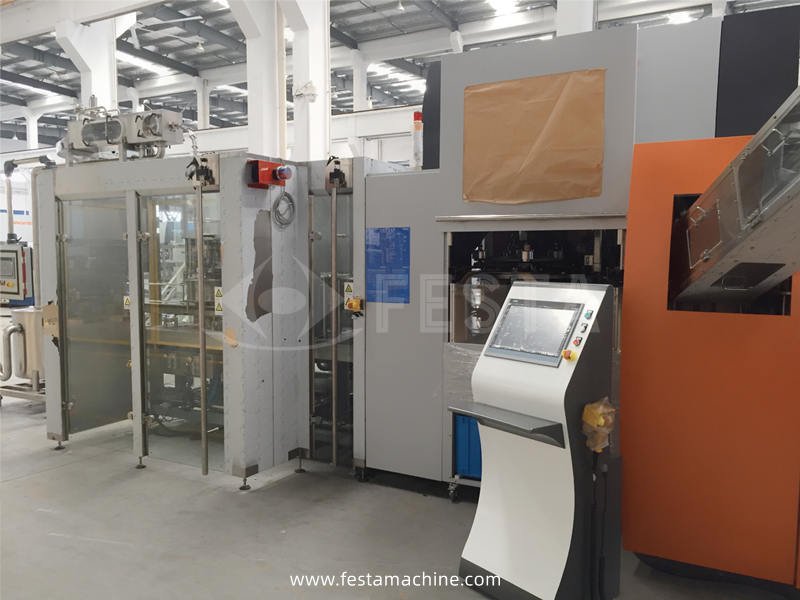
Main Compositions
- Preform feeding, sorting: The preforms are unloaded into the preform hopper and are then transferred to sorter by a preform elevator. The sorter conveys preforms to a feed rail, at the end of rail the preforms are captured by in-feed star-wheel. Then preforms are sent into heater. While the additional performs will fall down to perform conveyor installed below perform unscramble by perform rejecting wheel, which will return un-oriental performs to perform hopper. The whole process realizes automation control, high efficiency and no damage to perform.
- Ionized air de-duster: Due to static electricity action, some ash and microorganism will adhere to perform inside, which will affect final product quality. In order to get rid of it, ionized air de-duster is equipped in FESTA’s Combi. The ion generator will produce lots of positive and negative ion, after mixing with clean air, which will spray perform inside to neutralize the ash with static electricity and will be blown outside of perform. The ash will be drawn by negative pressure wind and be collected to one ash-collecting bag.
- Horizontal preform heating: The heating system is equipped with six-state red infrared ray heating lamps; adopt preform mouth downward heating technic to decrease influence of thermal flow. Moreover, cooling wind and cooling water channel can also installed to protect perform neck. During the heating process, the preforms constantly turn around themselves, so as to ensure an excellent and symmetrical heat distribution. Each oven module and each lamp can be adjusted with regards to position and power, thus assuring the maximum temperature curve. At the heating module outlet, a sensor detects the preform temperature and compares it with the temperature setting point; if the two values do not correspond, it will be rejected by rejecter.
- Blowing station: After leaving the heating oven, preforms are transferred by mechanically synchronized gripper of transfer wheel to the cam-controlled blow wheel. In blowing stations, there are three phases of stretch-blowing process: Stretching and pre-blowing, which occur simultaneously through the descent of the stretching rod and the supply of low-pressure compressed air. After pre-blowing, mid-blowing will be done and then final blowing with high-pressure compressed air, the bottles will take into their final shape and will be transferred to star wheel by gripper.
Filling and Capping Bloc
Main Compositions
- Transfer wheel
- Bottles are positively transferred by means of star-wheels modules.
- Positive transfer can handle any type of bottle without problems, including light weight, avoiding bottle jam and maintenance need.
- Draining basement
- Adopt roof type basement, not easy for ash to accumulate.
- Convenient for operator to clean machine.
- Filler
- Rotary wheel fully made of stainless steel SUS304.
- Filling valves are made of SUS316L.
- Adopt turbine flow meter type filling valve, non-contact with bottle, more hygiene.
- Cleaning dummy cup is equipped, thorough CIP can be done.
- Capper
- Adopt magnetic constant torque capping heads, defect rate is less than 0.2%.
- Cap distributing chute is equipped with reverse cap stop and reverse cap pick-out mechanism and the photocell switch is also installed to stop the capper when there is no cap inside the chute.
- The capper is equipped with bottle-feeding detection switch. When there is no bottle, cap-feeding will also stop, reducing cap loss.
- Centrifugal way of cap sorter is adopted to reduce caps friction.
- Cap inspecting system is installed on cap sorter to control on-off of elevator.
Technical Parameters
Blower
PRODUCTION DATA | ||
Mould Cavities | 6 pcs | |
Weight of Main Part | 17 T | |
Height of Machine | 3.4m | |
Preform Elevator | 4.5m | |
Capacity | 12000BPH (500ml) | |
Bottle Volume Range | 0.25-2.0L | |
Max. Bottle Height (below support ring) | 325mm | |
Max. Bottle Diameter | 110mm | |
Max. Diameter of Supporting Ring | 36mm | |
POWER SUPPLY | ||
Voltage | 415V, 50Hz | |
Installed Power | 160 KW | |
Power Consumption | 40KW | |
HIGH PRESSURE COMPRESSED AIR | ||
Air Inlet Pressure | 3.5-4.0MPa | |
Air Purification | According to ISO8573-1 standard | |
Compressed Air Consumption | 5.0Nm3/min | |
COOLING WATER | ||
Water Pressure | 0.6MPa | |
pH Value | 7-8 | |
Chiller for mold bottom | Cooling water flow | 6.0 m3/h |
Inlet temperature | 8-15℃ | |
Temperature difference between inlet and outlet | 3℃ | |
Chiller for Heater | Cooling water flow | 2.5 m3/h |
Inlet temperature | 17-22℃ | |
Temperature difference between inlet and outlet | 8℃ |
Filler-Capper
PRODUCTION DATA | |
Number of Working Stations | Filler 24, Capper 8 |
Rated Capacity | 12,000BPH (500ml) |
Filling Method | Gravity filling |
Suitable Bottle | Diameter:φ55-φ100 mm |
Height:160-310mm | |
Air Supply Pressure | 0.7 MPa |
Air Consumption | 0.8 m3/min |
Main Motor Power | 2.6 KW |
Working voltage (AC) | 380V |
Control voltage (DC) | 24V |
Weight | 5000Kg |
Tab Contentsssssssssssssssssssssssssssssss